鈦合金表面摻金屬類金剛石薄膜的摩擦磨損性能研究
發布時間:2023-02-10
PVD真空離子鍍膜的鈦合金強度高、密度低及耐腐蝕性能好且在中等溫度下機械性能穩定,已廣泛用于飛行、化工及生物醫療等領域,但鈦合金的耐磨性能差,對粘著磨損和微動磨損非常敏感,這嚴重影響了鈦合金結構的安全性和可靠性,并限制了其應用,因此,利用表面改性技術改善鈦合金的摩擦磨損性能倍受關注。
類金剛石(DLC)碳膜具有許多與金剛石相似或相近的優良性能,如極高的硬度、良好的摩擦磨損性能以及熱導率高和化學性能穩定等作為表面保護膜,DLC薄膜具有較低的摩擦系數,與許多材料配副的摩擦系數均在0.2以下,且具有良好的自潤滑特性。目前,DLC薄膜已用于光盤模具和計算機磁盤上,但是在工程構件,特別是在苛刻條件下的應用至今仍處于研究階段;且國內外有關類金剛石碳膜的摩擦磨損試驗研究大多集中于鋼基體上,對于鈦合金基體上制備類金剛石碳膜且在較大載荷下的摩擦磨損行為研究的報導較少。
本文作者采用陽極層流型矩形氣體離子源(AE公司直流電源)結合直流非平衡磁控濺射法,在Ti6A14V鈦合金基體上分別沉積摻鈦類金剛石碳膜和摻鎢類金剛石薄膜,并在高載荷下進行微動摩擦磨損性能對比試驗,以期為類金剛石薄膜在鈦合金表面的應用提供實驗依據。
1、實驗部分
基體材料選用單晶硅片、不銹鋼片(微觀結構測試用)及Ti6A14V(TC4)鈦合金(摩擦性能測試用)3種,鈦合金退火后顯微硬度為2.89Pa,其尺寸為D24mm×7.88mm,經磨平后表面粗糙度為0.8um。
利用陽極層流型矩形氣體離子源結合非平衡磁控濺射設備在鈦合金表面沉積類金剛石薄膜,所用氣體為99.99%高純氬及99.99%高純甲烷,分別采用金屬清洗液及無水乙醇超聲清洗鈦合金基底表面,烘干后放人真空室內,抽真空至5×10-3Pa,通氬氣至5×10-1Pa,用離子源結合直流偏壓濺射鈦合金表面;沉積時真空度為3×10-1Pa,直流偏壓為-100V,首先采用磁控濺射制備過渡層(2種薄膜的梯度過渡層工藝相同),然后用離子源離化甲烷成碳離子,同時分別開啟W和Ti磁控靶進行摻雜制備W-DLC和Ti-DLC薄膜,分別采用PHIQuan-teraSXM型X射線光電子能譜儀(XPS)及PHI-610/SAM型掃描俄歇(Auger)微探針分析薄膜的結構及其成分,采用6JA型干涉顯微鏡及金相法測量薄膜厚度,采用HXD-1000型顯微硬度計測量薄膜的硬度,采用WS97型涂層附著力劃痕試驗機測量膜/基結合強度。
摩擦磨損試驗在德國產Optimal-SRV型摩擦磨損試驗機上進行,采用面-面接觸形式,待測試樣(尺寸為D24mm×7.88mm,表面粗糙度Ra為0.8um)固定為被動摩擦副,對摩件材質為16Ni3CrMo(表面硬度>58HRC,表面粗糙度Ra為1.6um),尺寸為:凸臺D3.85mm×5.00mm,底臺D20.00mm×16.50mm,主動摩擦副做往復滑動,沖程0.25mm,頻率150Hz,加載載荷為50~600N,機油潤滑,試驗在室溫下進行,試驗過程中連續監測摩擦系數,通過Talysurf5P-120型表面形貌儀測量磨痕斷面深度,并以此計算磨損率,采用JSM5910型掃描電子顯微鏡(SEM)觀察分析磨痕表面形貌。
2、結果與討論
2.1薄膜結構和成分
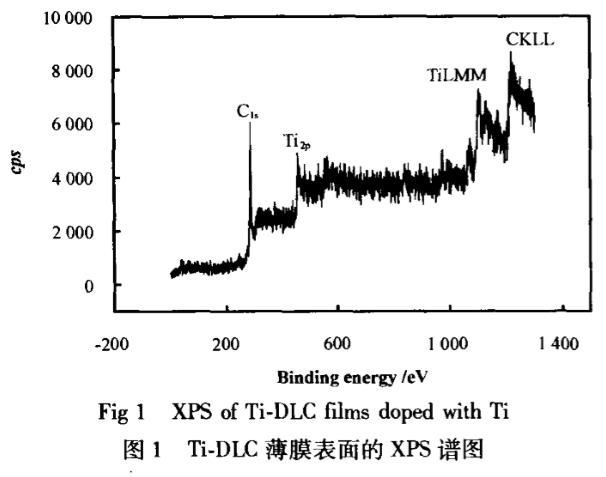
圖1所示為摻鈦類金剛石(Ti-DLC)薄膜的XPS譜圖可以看出:薄膜中除碳以外,還存在鈦(含量為6.8at%),Ti2p的特征峰位于455.1eV處,大于Ti值453.7eV,小于TiO,值458.7eV,可以判斷在非晶類金剛石薄膜中含有微晶TiC相,圖2所示為在鋼基體上所制備的Ti-DLC1(為了避免基體中Ti的干擾,采用鋼基體)樣品成分沿深度分布的曲線可見,膜層依次為Steel/Ti/TiN/TiCN/TiC/Ti-DLC,其中小于5at%的信號為儀器基底噪聲所致,同時,所含少量N可能是由于本底真空度(5×10-3Pa)不高而殘存一定空氣所致.在TC4基體上所制備的薄膜厚度約為2.81um,膜層的硬度HV0.1.25為6.51Pa(HV0.01.25=19.8GPa),膜/基結合力約44N。
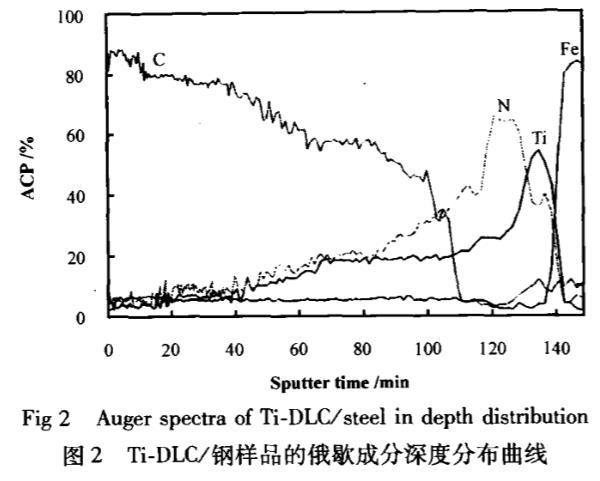
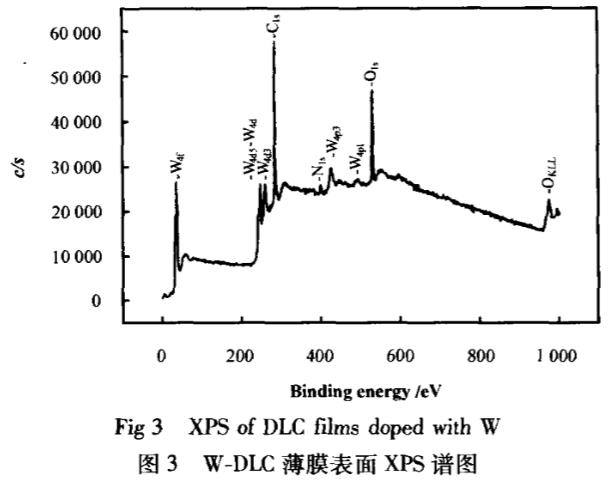
圖3所示為摻鎢類金剛石(W-DLC)薄膜的XPS譜圖可以看出:薄膜中除碳以外還存在鎢(含量為7.0at%),W4f的特征峰位于31.9eV處,大于w值31.4eV,小于WO2值32.8eV,而一般WC的處于31.5~32.8eV,可以判斷在非晶類金剛石薄膜中含有微晶WC相;同時薄膜中還含有少量氧及氮,估計是表面吸附污染所致,其梯度過渡層與Ti-DLC相同,只是最表層為W-DLC.在TC4基體上制備的薄膜厚度約2.83um,膜層硬度日HV0.1.25為8.78Pa(HV0.01.25=24.7GPa),膜/基結合力為60N。
2.2摩擦磨損性能
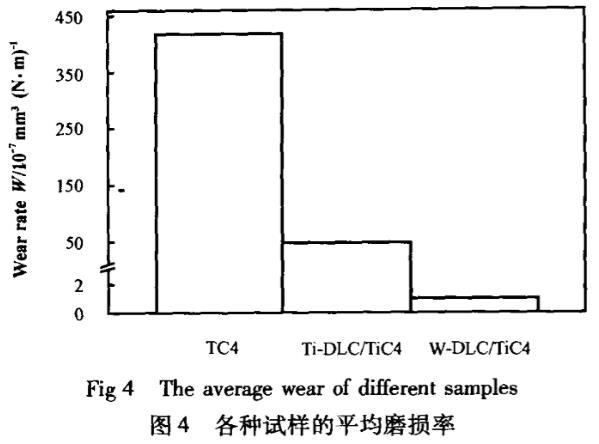
圖4所示為TC4基底、Ti-DLC/TC4及W-DLC/TC4薄膜的平均磨損率(該數據是在保載條件下計算出的,分別為TC4在200N摩擦15min;Ti-DLC/TC4在200N摩擦150min;W-DLC/TC4在300N摩擦1200min),可見:TC4基底的磨損率遠高于經DLC涂層處理的試樣;而在DLC涂層的處理中,W-DLC薄膜的磨損率更小,表現出良好的耐磨性,這是由于表面經DLC處理后硬度明顯增大,其整體承載能力增強,故其磨損深度較小,對基體材料起到了有效的保護作用,而W-DLC/TC4的硬度最高,且由于W-DLC膜層中含有WC微晶,故其體現出更優良的耐磨性。
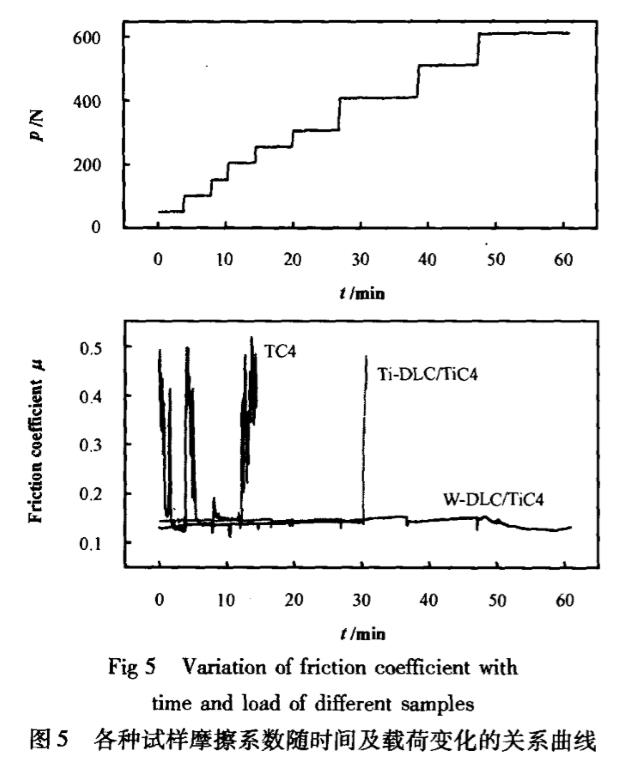
圖5所示為TC4基底、Ti-DLC/TC4及W-DLC/TC4薄膜在漸進加載條件下與16Ni3CrMo鋼對摩時,摩擦系數隨時問變化的關系曲線,圖中上半部為所加載荷隨時間的漸進方式,下半部為各樣品所對應的摩擦系數,可以看出:TC4基底的摩擦系數明顯高于表面經DLC處理的試樣,存在較長的“磨合期”;當載荷增至200N時,摩擦系數在0.25~0.50之間劇烈變化,當載荷超過200N時,由于摩擦力太大,已經不能保證試驗的沖程距離而停止試驗,而對于表面經DLC處理的2種涂層,由于其主要成分為非晶碳,少量的硬質TiC或WC微晶彌散于非晶碳中,在載荷小于400N下對涂層的摩擦系數影響較小,2種涂層的摩擦系數基本穩定在0.13~0.15之間,沒有大幅起伏變化和明顯“磨合期”.當載荷超過400N后,Ti-DLC/TC4的摩擦系數急劇升高,這主要是由于樣品的表面粗糙度較高,在上、下試樣間容易產生局部高接觸應力;當接觸應力高于涂層承受能力時,則造成涂層的部分“坍塌”和剝落,使兩者從邊界潤滑磨損轉變為微研磨磨損和與基底的粘著磨損,導致摩擦系數升高,W-DLC/TC4薄膜的摩擦系數直到載荷600N時均無顯著變化,這主要是由于W-DLC/TC4薄膜的硬度和承載能力較高、膜/基結合強度較好,涂層沒有出現“坍塌”和剝落現象;而載荷越高,摩擦系數越小,這與摩擦過程中DLC膜層在高載荷作用下的石墨化有關。
2.3磨痕表面分析
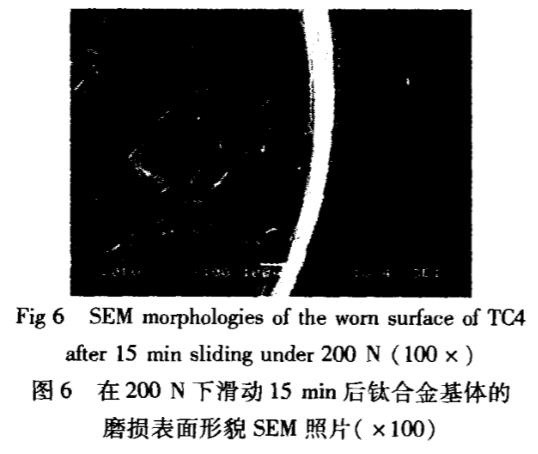
圖6所示為TC4基底在漸進加載(漸進方式如圖5上半部)至200N保載滑行15min后(不能繼續試驗)的磨損表面局部形貌SEM照片可見:其磨痕表面粘著痕跡明顯,主要為粘著磨損,并伴有少量磨粒磨損且磨痕較深,這主要是由于在加載初期,TC4表面氧化生成脆性較大的氧化鈦膜,在摩擦過程中出現疲勞裂紋,裂紋隨摩擦的繼續而擴張,隨著顆粒剝落形成磨粒而導致磨粒磨損¨.加載至200N并保載滑行15min后,由于基體較軟,承載能力不足而與偶件粘著,由于以粘著磨損為主,且伴有少量的磨粒磨損,故其的磨損率和摩擦系數較高。
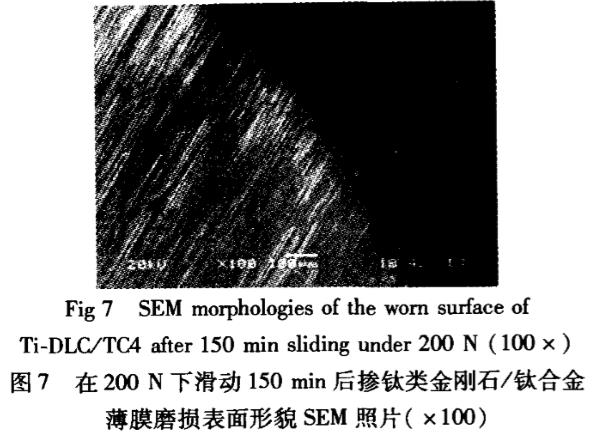
圖7所示為Ti-DLC/TCA薄膜在漸進加載(圖5上半部方式)至200N、保載滑行150min后(摩擦系數突變)的磨損表面局部形貌SEM照片可見:在磨痕表面粘著痕跡極少,以磨粒磨損為主,磨損區域與未磨損區界面為逐漸過渡,磨痕較淺,這主要是由于Ti-DLC/TC4薄膜/基較硬,承載能力較強,但膜層在較高載荷下,受膜/基結合強度不高及內應力的影響,摩擦-定時間后出現疲勞裂紋,繼而出現顆粒剝落而形成磨粒,導致磨粒磨損;而在局部磨損嚴重區域與偶件出現粘著現象,其原因是由于當局部接觸應力大于薄膜的承載能力時造成部分膜層“坍塌”或剝落,因此,Ti-DLC/TC4薄膜比TC4基底的磨損率和摩擦系數低、失效時間長。
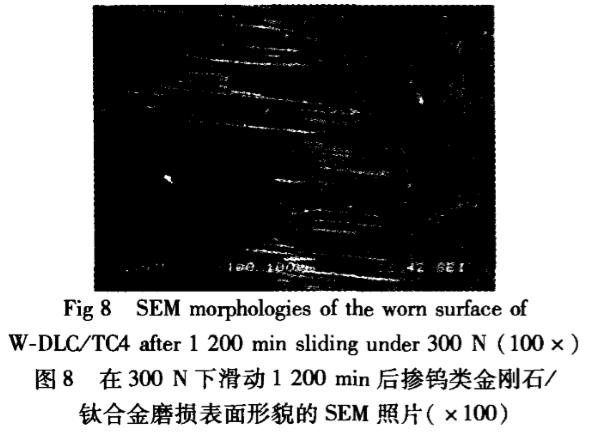
圖8所示為W-DLC/TC4在漸進加載(漸進方式如圖5上半部)至300N(為了加速試驗,選用更高載荷)保載滑行1200min后(未完全失效,停止試驗)的磨損表面局部形貌SEM照片可見:在磨痕區域主要為滑動磨損,磨粒磨損痕跡較少,磨痕很淺,這主要是由于W-DLC/TC4的承載能力較高,膜層硬度高、膜/基結合強度大的緣故,因此,經過更高載荷、更長時間后,W-DLC/TC4體現出比Ti-DLC/TC4更優異的耐磨性。
3、結論
a、TC4基底表面經DLC薄膜處理后的硬度明顯增加,其整體承載能力增強,類金剛石薄膜起到了有效的保護作用。
b、摻金屬類金剛石薄膜具有良好的抗磨減摩性能,在膜層承載能力范圍內,載荷越大,DLC梯度薄膜的摩擦系數越小。
c、摻雜w元素的W-DLC/TC4薄膜由于在薄膜中形成WC微晶,有利于提高膜層的耐磨性及其硬度和膜/基結合強度,具有更高的承載能力及更優異的抗磨性能,更適合于易磨損器件的表面改性。
作者:林松盛 ,代明江 ,侯惠君 ,李洪武 ,朱霞高 ,林凱生 ,牛仕超
聲明:本站部分圖片、文章來源于網絡,版權歸原作者所有,如有侵權,請點擊這里聯系本站刪除。
返回列表 | 分享給朋友: |